Mazda MX-30 multi-tone painting process—environmentally and people-friendly
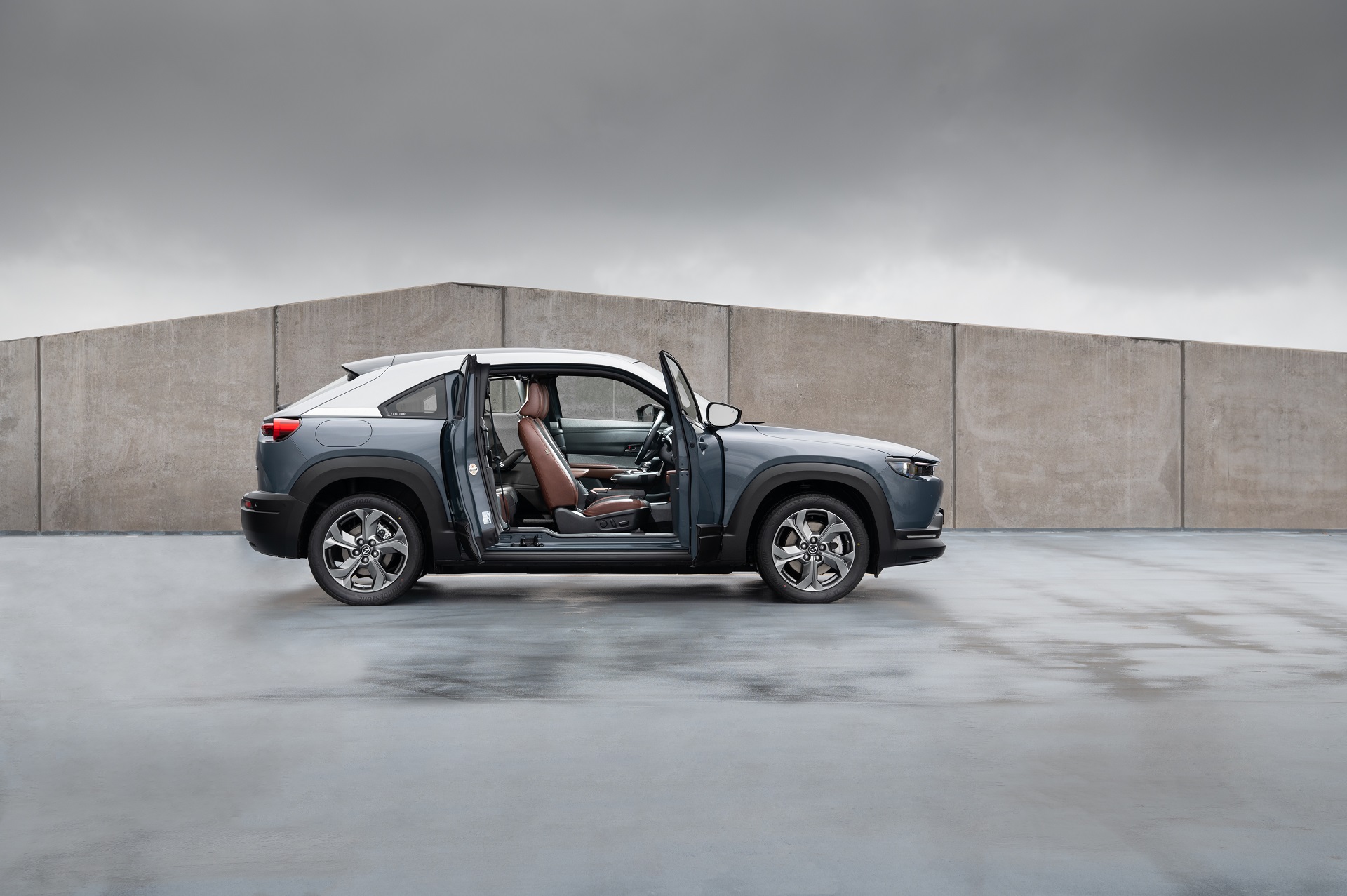
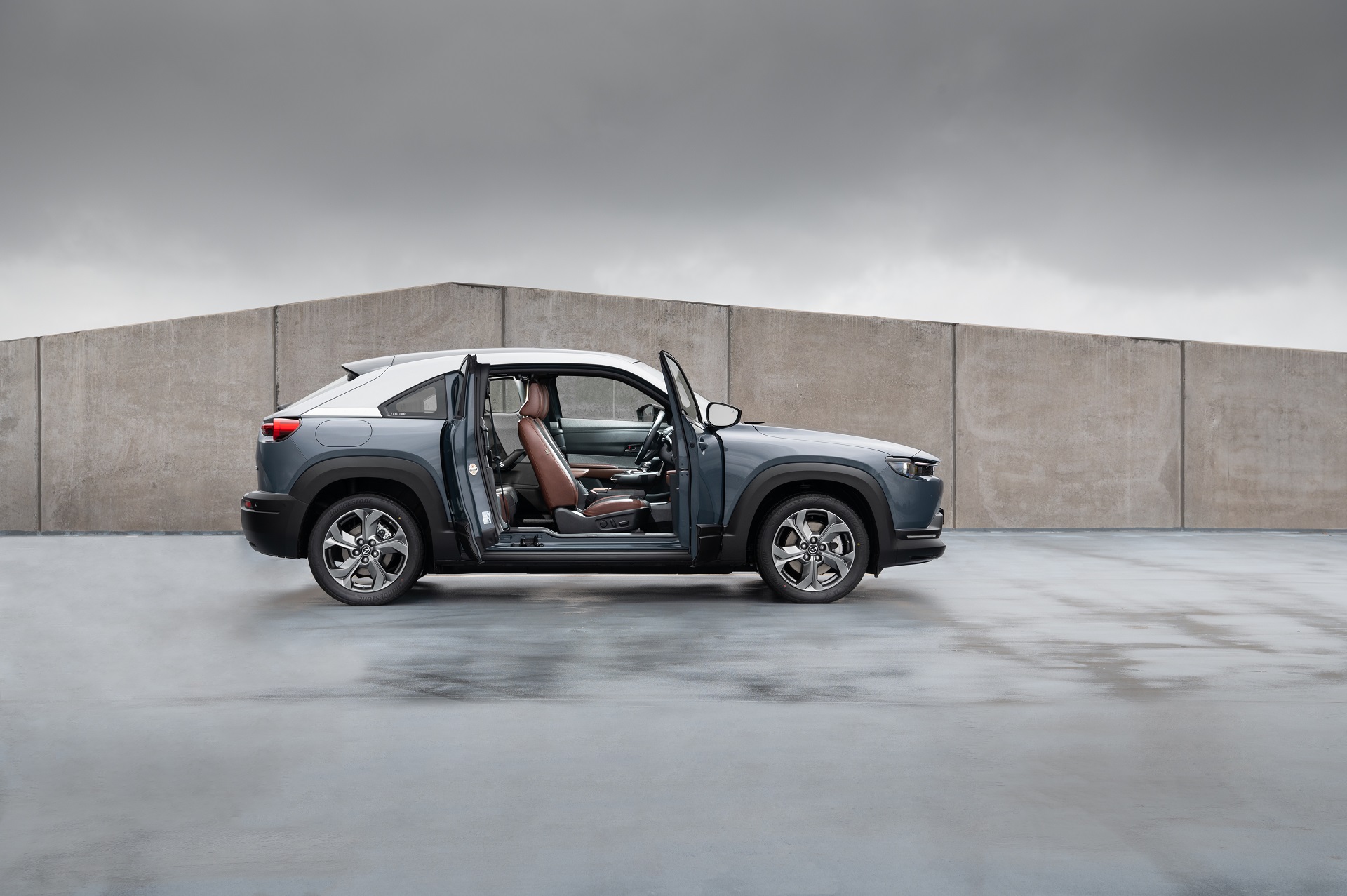
The immediately recognisable "MX" prefix is reserved for Mazda models that take on the challenge of creating and delivering new value, without being bound by the conventional wisdom of vehicle types or the era.
Just as the Mazda MX-5 – beloved the world over for more than 30 years – is the embodiment of the "MX" name, breaking the stereotype that open two-seaters are unmarketable and rekindling the lightweight open two-seater boom around the globe, the Mazda MX-30 plays a leading role in Mazda's electrification efforts to achieve carbon neutrality.
Available as a fully electric vehicle – the brand’s first mass-produced EV – or with the innovative M Hybrid e-Skyactiv G powertrain mild hybrid system, the MX-30 challenges the creation of new value. The exterior is uncompromisingly simple to emphasise the vehicle's beauty as a solid mass, while the cabin design expresses lightness with freestyle doors and multi-tones, further pushing the boundaries of the “KODO: Soul of Motion” design.
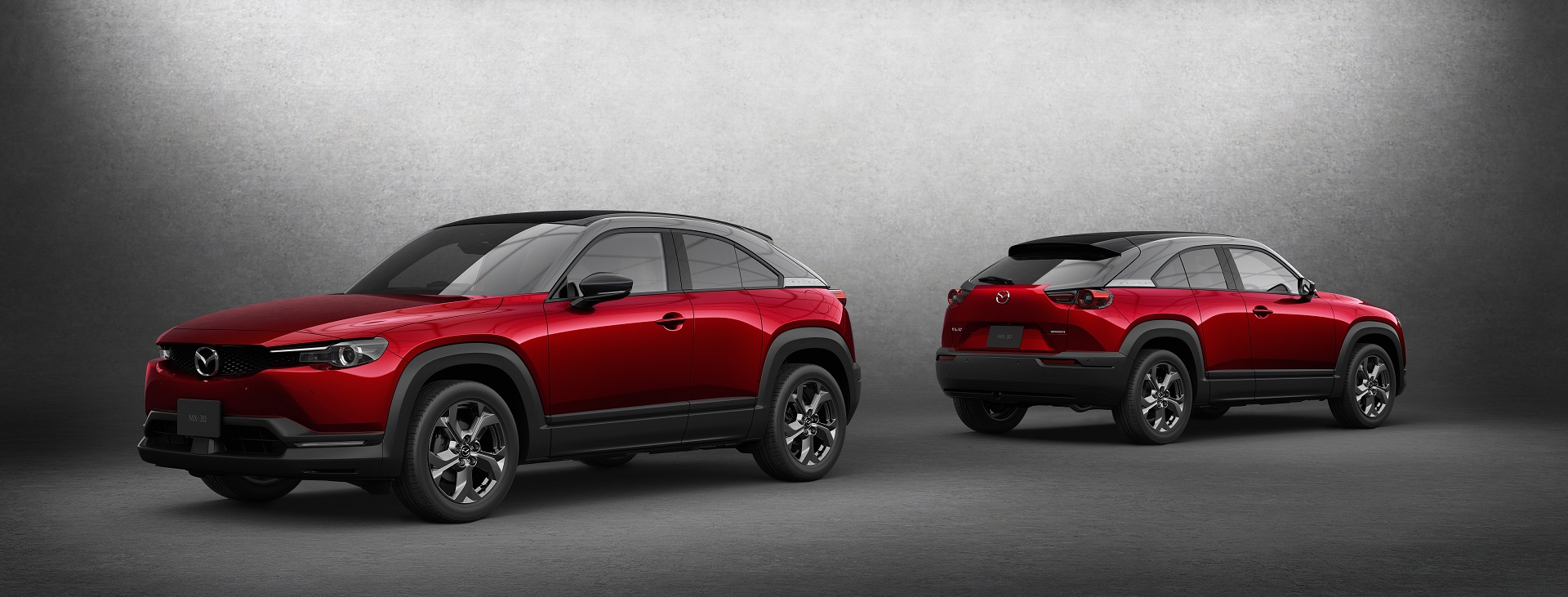
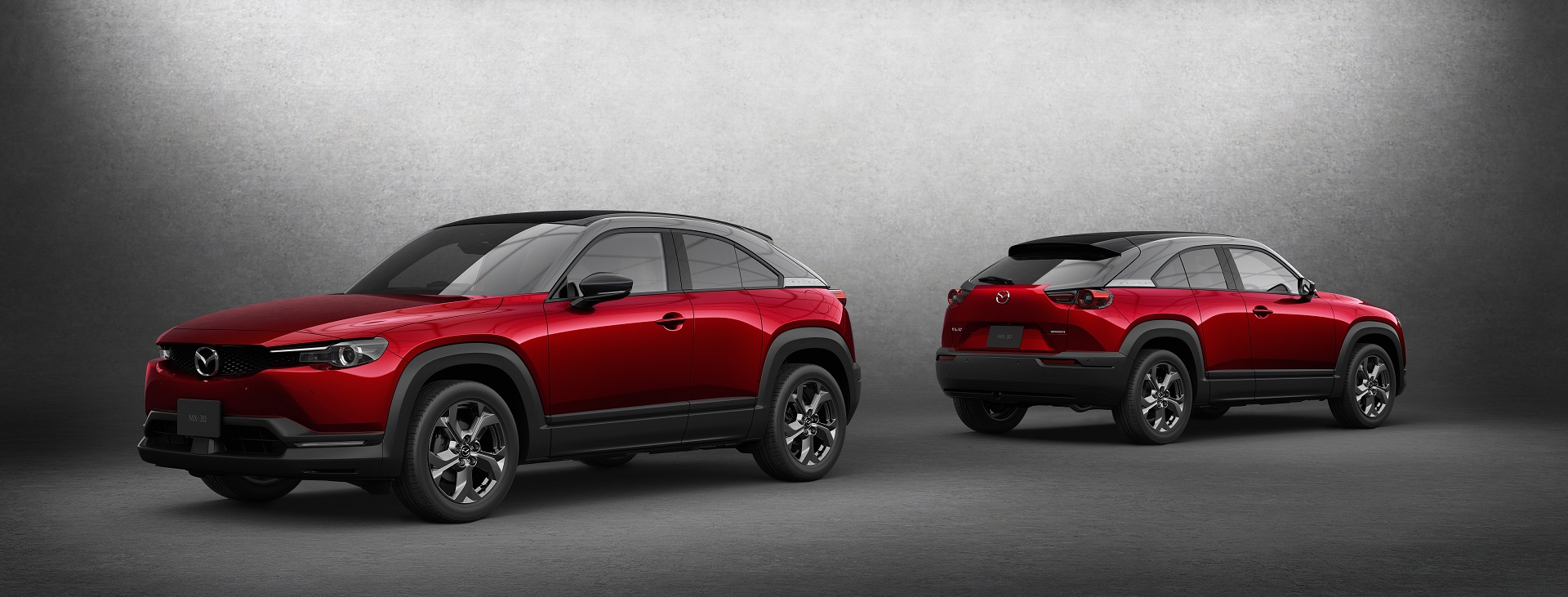
A selection of attractive 3-tone paint finishes – Ceramic metallic, Polymetal Grey and Soul Red Crystal – add more flair and individuality to the design. But there’s much more to these hues than meets the eye, with Mazda refining the multi-tone paint process to reduce CO2 emissions and energy consumption in the manufacturing area, while also improving the comfort of the workers engaged in the inspection process.
These two innovations form part of the brand’s Sustainable “Zoom-Zoom” 2030 philosophy, in which Mazda aims to realise a sustainable future where a beautiful earth, an enriched society and cars coexist through the joy of driving. Mazda has also set the goal of becoming carbon neutral throughout its supply chain by 2050, and in the area of manufacturing, the aim is to achieve carbon neutrality at all global plants by 2035.
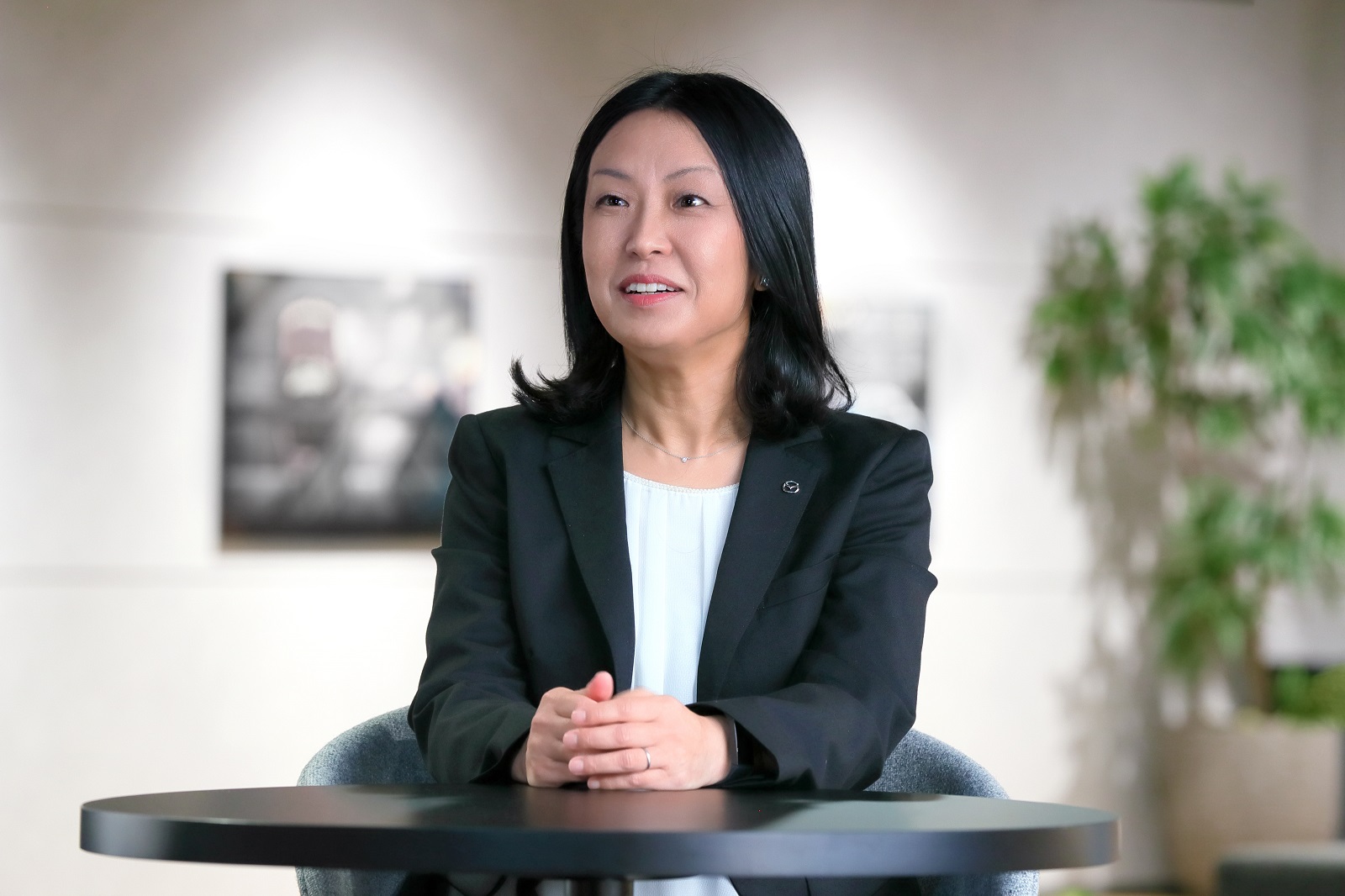
MX-30 Program Manager Wakako Uefuji
“The 3-tone multi-tonal paint schemes is available on the MX-30 in multiple variations depending on the different areas to be painted. The paint is applied to the base body colour on a regular paint line, and then layered on a dedicated multi-tone line to achieve impressive colour combinations. In this process, we believe that our mission is to simultaneously reduce environmental load with an aim to achieving carbon neutrality while creating vehicles that satisfy our customers. To this end, the MX-30 multi-tone paint shop is introducing new technologies to reduce environmental load, and is working to achieve worker-friendly work processes based on a human-centred approach. Let us introduce you to some of these initiatives.”
Preparation for multi-tone painting
Entrance to the paint shop
The paint shop is located in Ujina Plant No. 1, almost exactly in the centre of Mazda's main plant in Hiroshima Prefecture.
This building, where entry is conditional on changing into special uniforms that suppress static electricity and do not allow even miniscule amounts of dust to fly from one's clothes, is the factory building where body painting is performed. After proceeding through a passageway covered with adhesive walls on all four sides and passing through a double door with air blowing all over your body, you finally enter the area where the painting is done.
Here, different vehicle bodies, such as the MX-5 and CX-5, are painted in different colours on the same paint line. Mazda's unique Aqua-Tech Paint System, which uses water-based paints, incorporates world-class technology to reduce environmental load. One floor is located slightly apart from the row of numerous body shells going through the standard painting process. This floor is the dedicated MX-30 multi-tone paint line. One MX-30 is pulled from the row and brought to the floor along a rail that looks like a pull line. Special work is done here for customers who have opted for 3-tone colours. Upon arrival at the clean room booth, the MX-30 is first subjected to a masking process that precisely separates the areas to be painted over. Four expert workers apply masking tape and vinyl sheets while applying templates, and the masking is done with great dexterity.
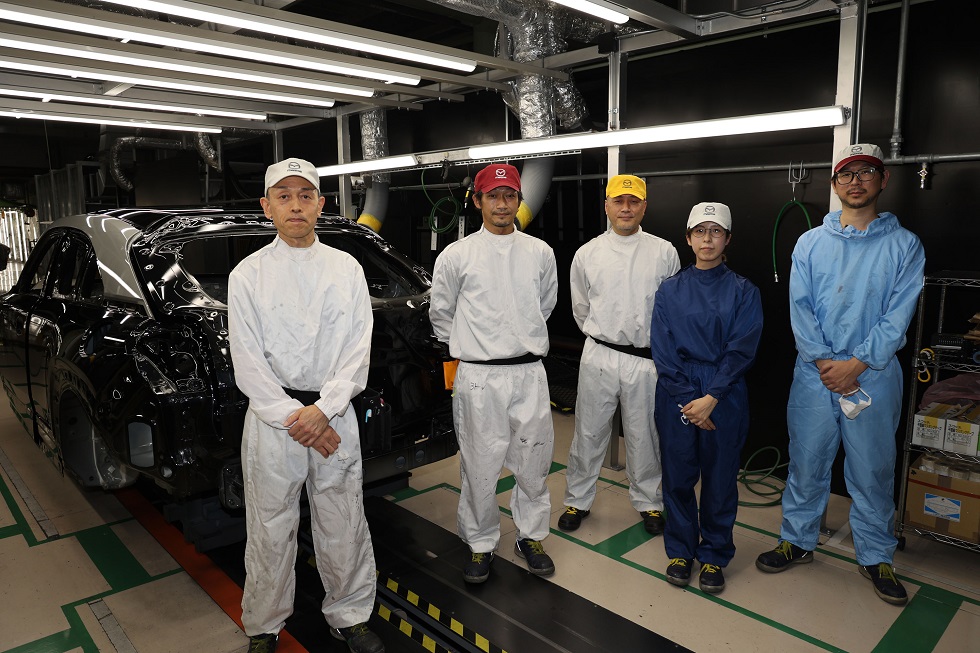
“As a worker in charge of a process that is not mechanised, I am always aware of the fact that my work directly affects the finish of Mazda vehicles delivered to customers. At the same time, I also feel the joy of seeing customers driving around the world in Mazda vehicles that we have worked on. That is why we put our heart and soul into this extremely detailed work.”
The latest energy-efficient painting technology
Once the masking is completed, the body is again pushed by the operator on rails to a special paint booth. This special multi-tone paint booth is divided into four rooms, each of which is divided into four sections. From the one nearest the entrance, there is a "preparation zone" where fine dust is completely removed, a "painting zone" where a robot does the painting, a "setting zone" where the paint is acclimated, and a "drying zone”. In automotive painting, paint is sprayed evenly in a fine mist and then heated to a high temperature to dry, forming a strong film that keeps the beautiful shine of the car body protected for a long time. These paint spraying processes require large amounts of energy, but with the newly developed paints and new compact paint booths, Mazda has succeeded in significantly reducing CO2 emissions.
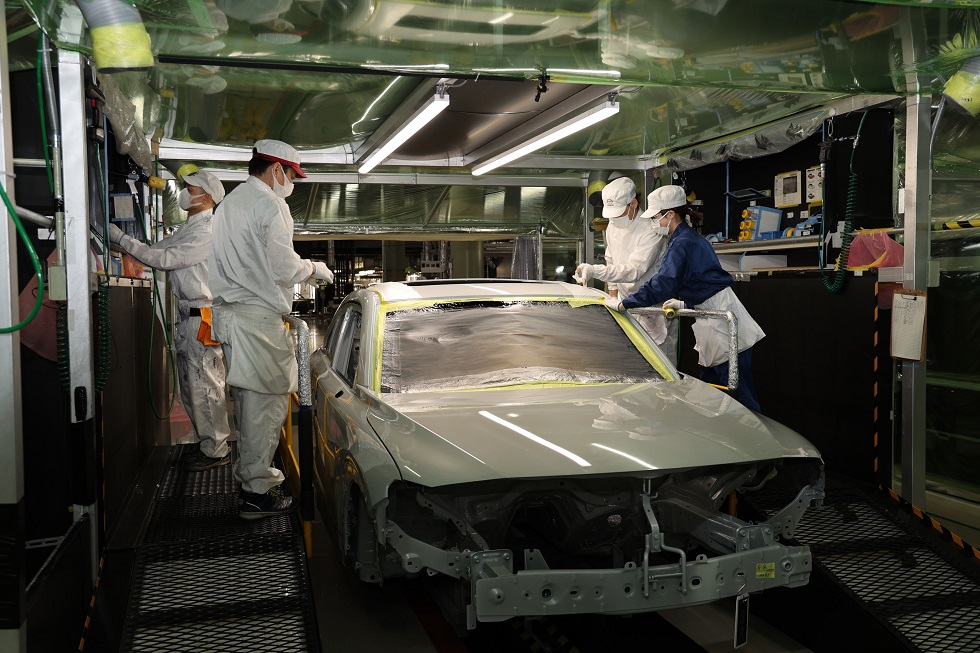
Masking operation
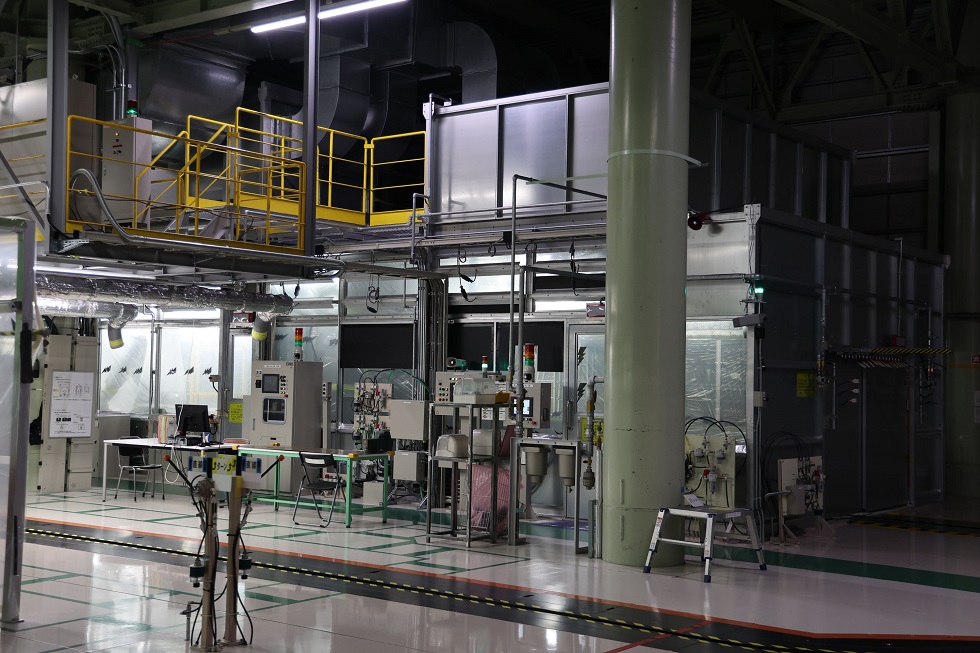
On the right, the entrance to the painting booth
The masked MX-30 is brought in front of the paint booth entrance door and pulled into the "preparation zone," where the body is subjected to a strong air shower blown from the ceiling. The first door opens and the MX-30 is pulled into the "preparation zone," where the body is subjected to a strong air shower blown from the ceiling. Eventually, the door to the next zone inside the paint booth opens, and the MX-30 moves into the "painting zone," where it is sprayed with a light mist of paint. This is one of the processes where Mazda has introduced new environmental load reduction initiatives in the multi-tonal painting process. The spray paint gun used here is characterised by its ability to concentrate paint in the required areas and reduce environmental load by preventing paint loss. This painting technology is also supported by precise millimetre-by-millimetre control of the distance between the nozzle of the spray paint gun attached to the end of the robot's arm and the surface of the body.
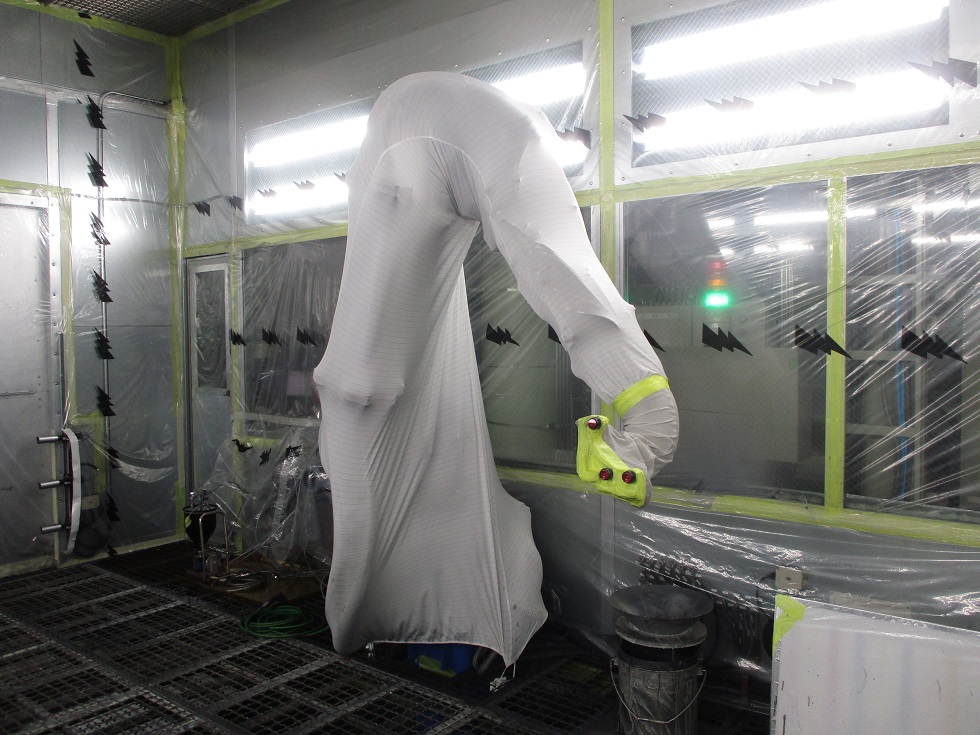
Spray Paint Gun
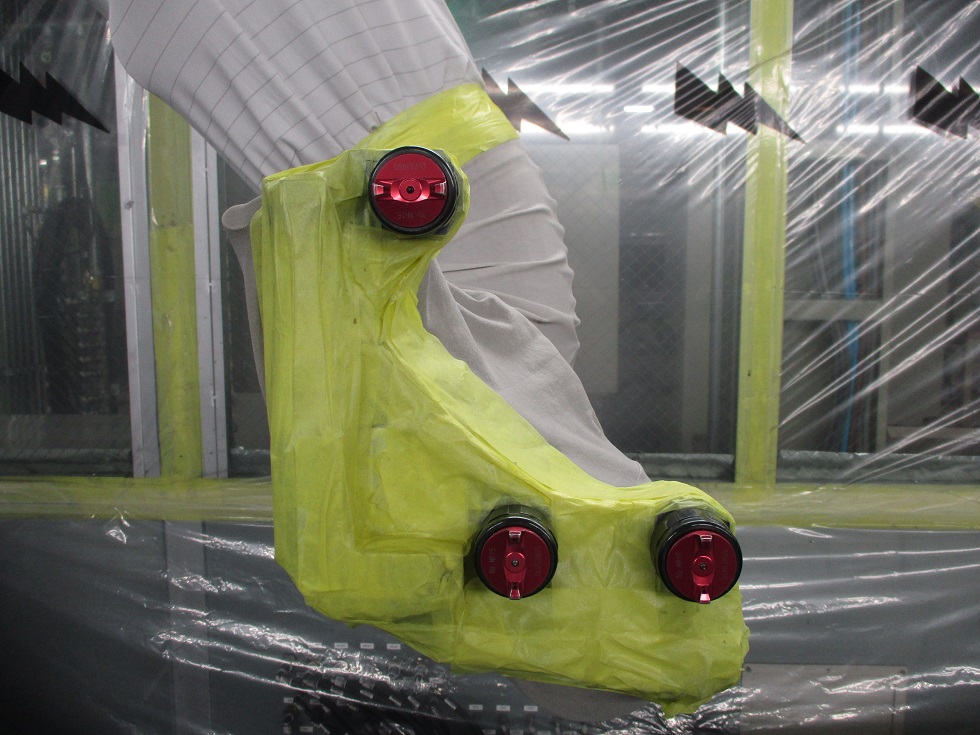
Spray paint gun nozzles
Precise control of light reflection
After the MX-30 has been painted, it proceeds to a process called setting. In this process, which is used to adjust the beauty of the paint film to the desired level, time is spent to ensure the orientation of the light-reflecting materials in the paint, such as aluminium and mica (quartz), and adjusted to the desired angle. This process precisely aligns multiple factors such as paint density, the size and shape of the metal flakes, which are adjusted on a microscopic scale, and the thickness of the paint to be sprayed.
Energy reduction through low temperature curing paint
The final step in the four-step multi-tonal painting process is the drying process. Normally, the drying process requires a lot of energy to generate heat, but Mazda has succeeded in drastically reducing energy consumption in the process by introducing a new paint that "paints beautifully and firmly at a low temperature”.
Drying zone is covered with insulation due to high temperatures
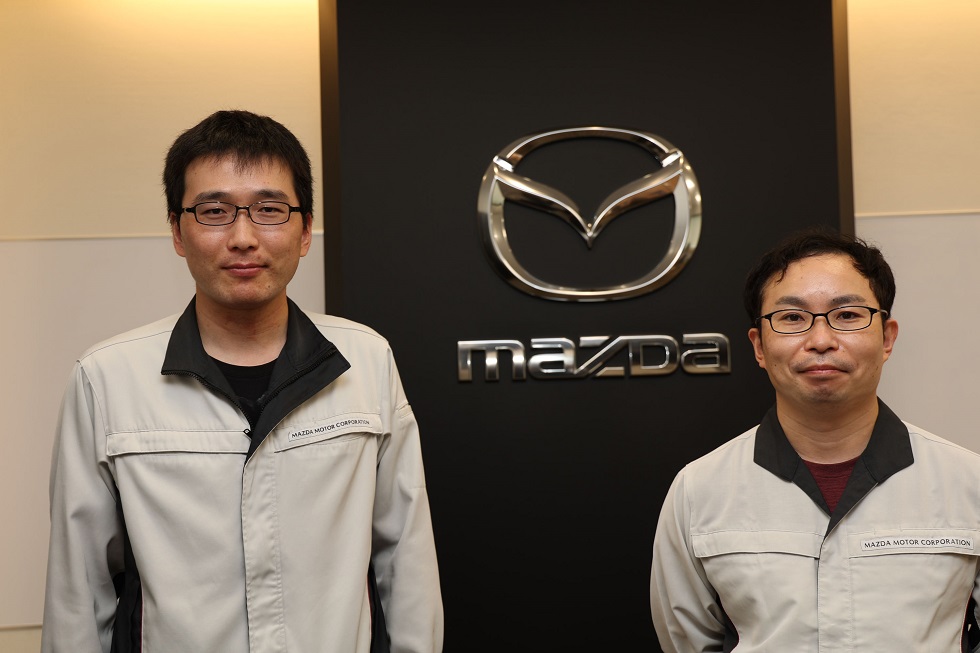
Takahiro Matsumoto and Hiroaki Hattori, Paint Technology Group, Vehicle Engineering Dept.
“To reduce energy consumption in the painting process, it is necessary to dry the paint at lower temperatures. The paint used in the normal painting line is heated to 140°C to form a film of the quality we require. On the other hand, the paints used in the dedicated multi-tone paint line are two-component curable paints that can be baked and dried at 80°C. This is 40% lower than the previous painting line. Despite 40% lower temperatures than those used previously, the paint film will meet all the quality requirements of Mazda vehicles, including protection of the vehicle body, beautiful gloss and colouration.
In addition to developing a two-component curable paint that offers significant energy savings, production technology engineers are trying two additional innovations. First, they designed the drying zone to be as compact as possible to reduce the energy consumed in raising the temperature of the space. The system also utilises two types of heat sources, a compact infrared heater and warm air, which can overheat only those parts that need drying, and a temperature increase control program tailored to the car model and paint colour.
Compared to the conventional 3-tone painting process that loops the process, the new system reduces CO2 emissions by 37%. In 2002, Mazda introduced the “three-wet-on” painting system, which significantly reduces CO2 emissions compared to conventional oil-based paints. Then, in 2009, Mazda introduced the Aqua-tech Paint System, Mazda's proprietary water-based paint. Normally, water-based paint requires more energy to dry than oil-based paint, resulting in an increase in CO2 emissions, but Mazda has devised a drying process that does not increase CO2 emissions. In this way, technologies for reducing the environmental load of painting have advanced dramatically over the past 20 years.”
Inspection process that reduces the burden on workers
After the MX-30 is painted, the same process is repeated one more time for the 3-tone paint job. All the bodies that have completed the multi-tonal painting process then go to a dedicated inspection line. All Mazda vehicles, not just the MX-30, undergo a thorough quality check by trained paint workers with discerning eyes. Conventional inspection lines consist of tunnel-shaped black walls lined with straight LED lights. This strong contrast makes it possible to clearly reveal even the slightest irregularities in the paint, foreign objects, and unevenness. However, such an environment is like being continuously exposed to a spotlight, and for the people working on it, it is a strenuous and heavy workload. In the past, we have managed schedules so that workers do not spend long hours in such an environment, but in the area where the MX-30 is being used for multi-tonal painting, Mazda is taking the challenge one step further.
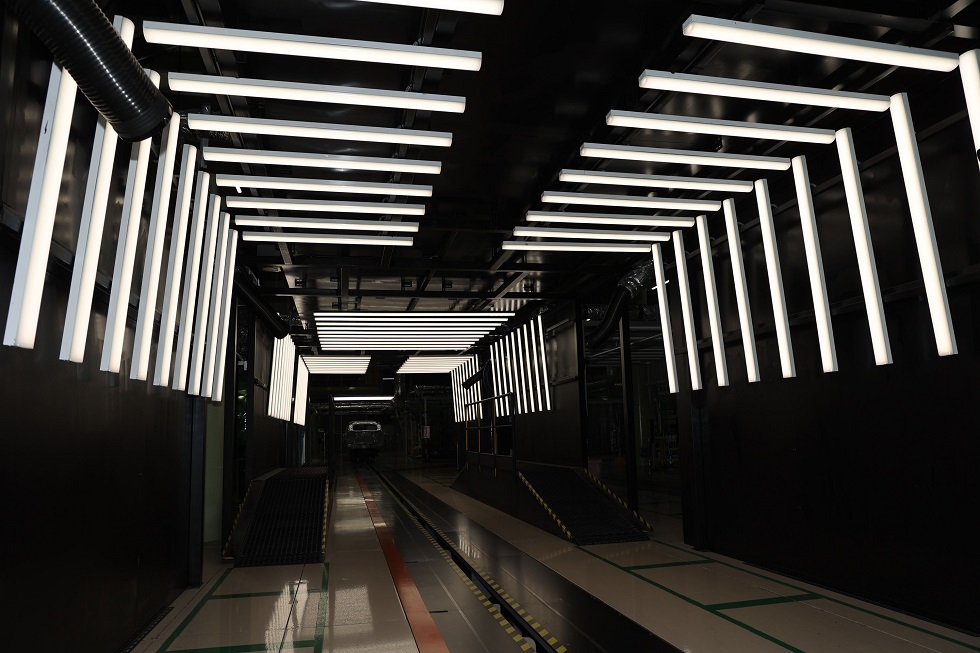
Inspection line where the car body goes through after multi-tone painting
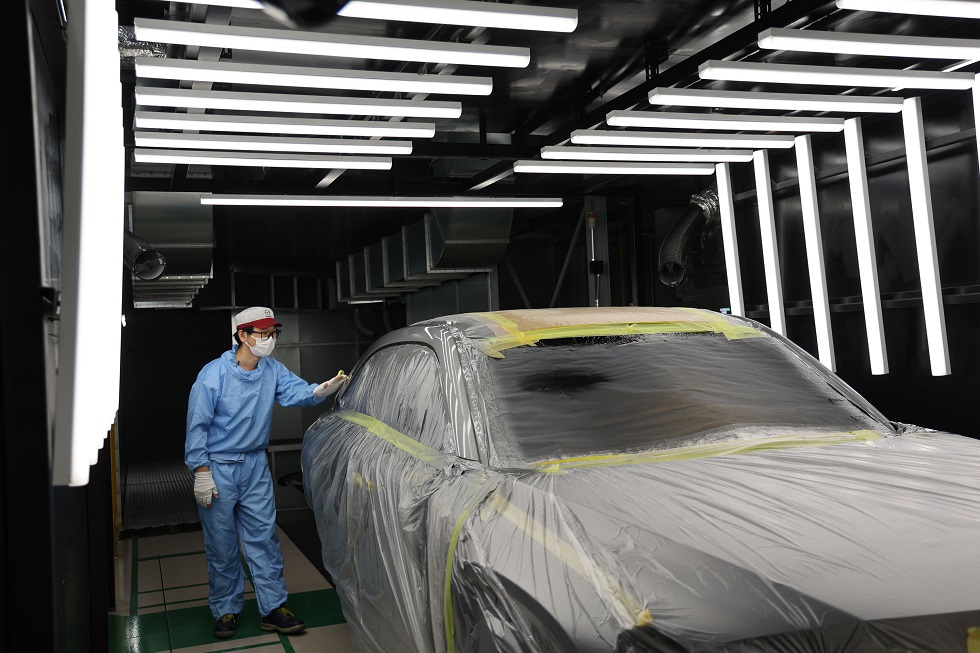
Inspection is done visually by the operator
Program Manager Uefuji says of the MX-30's multi-tonal paint inspection process; "This zone reduces the burden on the workers by providing only the necessary illumination to the required areas and by setting the illumination level lower than in the existing inspection zones. The colour of the walls of the inspection line is black in order to block disturbances and make the inspection surfaces stand out to ensure the same high level of quality control as before. In addition, the illumination intensity and colour temperature can be changed as needed. Mazda's concept of technology to reduce environmental load also includes the improvement of the working environment.
Mazda is an automobile manufacturer that creates people-friendly vehicles. The people we are referring to here are, of course, the customers around the world who love Mazda vehicles and the joy and smiles the cars bring to their faces and, by extension, their fulfilling lives. At the same time, we believe that the same applies to our colleagues who work day in and day out to deliver such Mazda vehicles to the world.”
After passing through the inspection line, the multi-tone painted MX-30s proceed along the rails to join the line of other car bodies. They are then headed for the next stage of the assembly process.
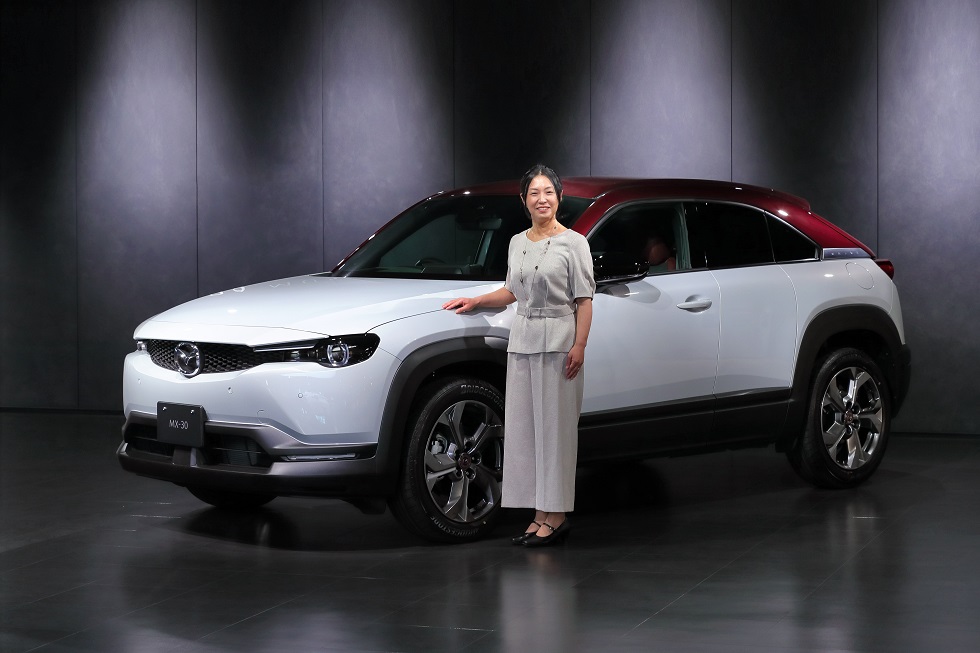
Wakako Uefuji, Program Manager of MX-30
“For whom and what are we really talking about and tackling when it comes to environmental issues? I think it is very important to be well aware of the answers to these questions. For Mazda, the answer is clear. It is that we want people to enjoy fulfilling lives through cars. In order to pass on to the future a planet where people can live happily forever, we must first of all protect the environment. At the same time, we want our customers to lead enriched lives through the "joy of driving”. How can we achieve both of these goals? At Mazda, the MX-30 is at the forefront of these efforts. While offering body colours that customers can't help but admire, we aim to create cars that are friendly to the global environment as well as to their creators. This is our aspiration for the MX-30.”
Use of solar power generation to charge the MX-30 drive battery
Efforts to reduce the environmental load of the MX-30 manufacturing process are not limited to the multi-tone painting process. A solar power generation system on the roof of the product warehouse at Mazda's main plant, which started operation in July 2021, is also making a significant contribution to the company’s reducing environmental load.
With a total of 2,698 photovoltaic panels covering a total area of 11,000 square metres, the facility has the capacity to generate 1.1 MW of electricity. The power generated here is used to charge the drive batteries needed to ship the MX-30, and is also allocated to power the plant's offices and other facilities. In this way, we are actively promoting the use of green power in order to achieve carbon neutrality at Mazda’s global manufacturing plants by 2035.
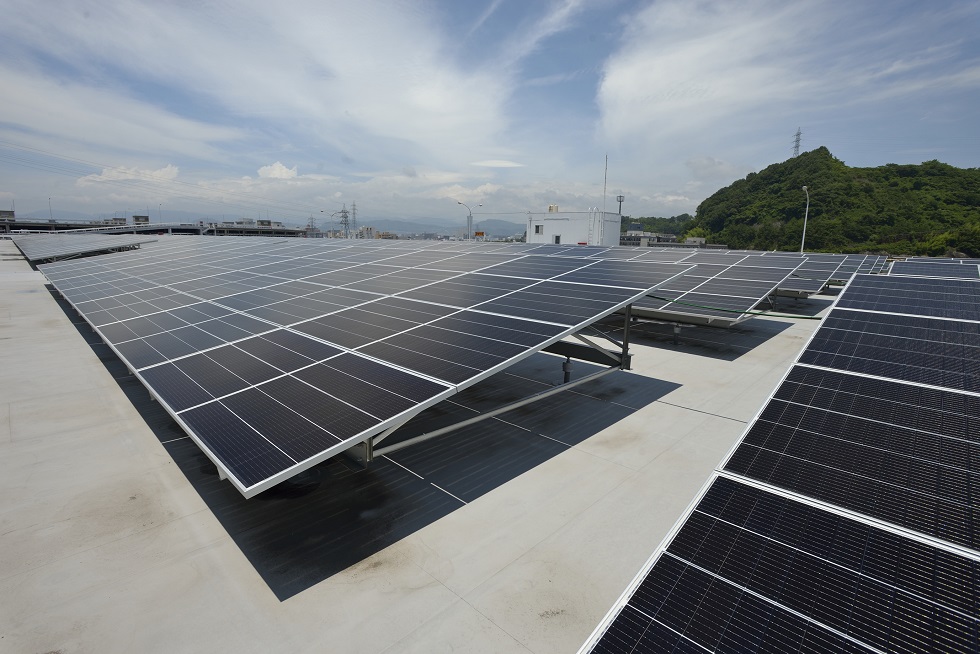
Solar power generation equipment
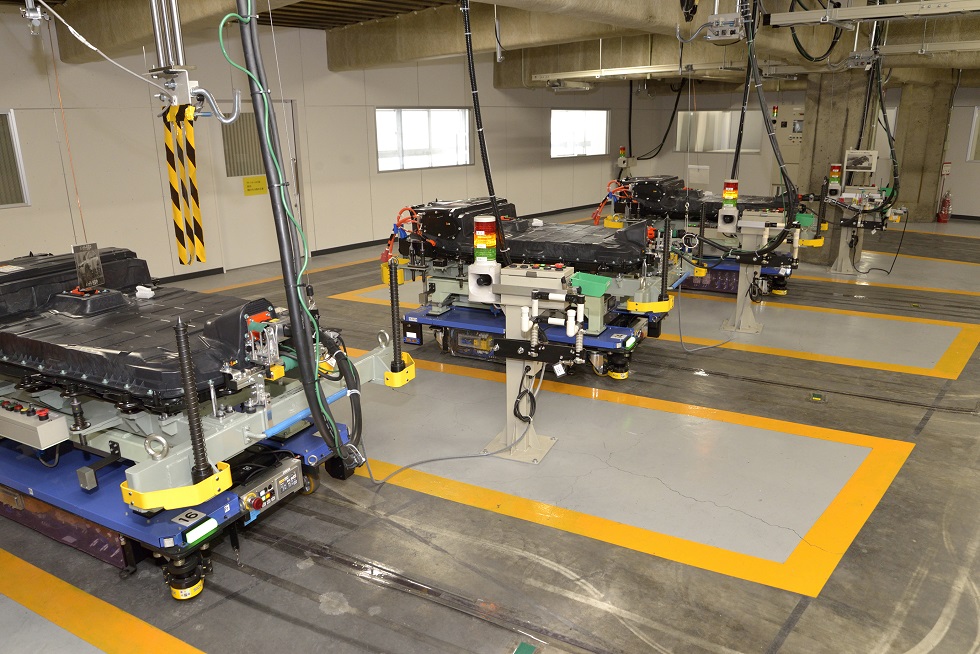
MX-30 EV Model Drive Battery Charging Plant